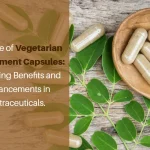
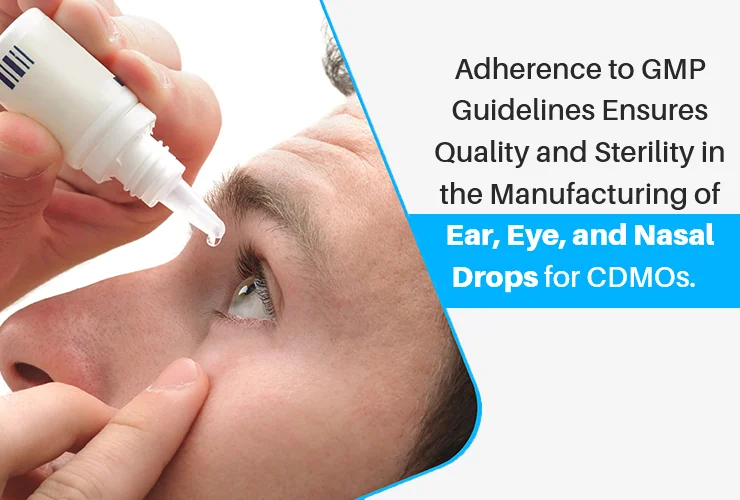
An Introduction
Drug manufacturing is a tough task that is the work of skilled professionals. The pharmaceutical industry is always looked up for trust, reliability, and authenticity which is showcased through their yield of medications that help to sustain the same. Drug manufacturing has to undergo tough manufacturing technicalities, stringent tests, and strict adherence standards to get authentication as the final drug product to be used by the consumers. One such compliance standard is GMP i. e. Good Manufacturing Practices.
GMP & CDMOs
As contract development and manufacturing organizations (CDMOs) are responsible for producing a wide variety of pharmaceutical products, it becomes paramount to adhere to Good Manufacturing Practices (GMPs) guidelines set by regulatory authorities like the US Food and Drug Administration (FDA) to ensure the safety, quality, and effectiveness of the products.
In the manufacture of the ear, eye, and nasal drops, adherence to GMP guidelines becomes even more critical as these products are intended for delicate parts of the body, and any contamination or mistakes in the formulation can have severe consequences for patient safety.
GMP guidelines dictate that every aspect of the manufacturing process, from raw material selection to final product packaging, is designed to ensure that the ear, eye, and nasal drops are manufactured consistently, meet quality standards, and are free from contamination.
In the production of these pharmaceuticals, contamination from bacteria or other microorganisms can occur if not managed and controlled properly. The manufacturing environment needs to be controlled to avoid cross-contamination between products and equipment.
The use of sterile equipment, sterilization of raw materials and final product packaging, and validation of process control ensure the purity and sterility of the final product. Adherence to GMP guidelines also involves developing and implementing a quality management system that monitors and records every step of the production process to detect and mitigate potential issues. Most eye drops are suspensions or solutions, in fluid, which states that most of the optical engineering process begins with water for injection. Some CMOs create their water for injection on-site by cleaning water and a disinfected environment, while others get disinfected, clean water. This is one cause why ophthalmic manufacturing conveniences need to abide by GMP guidelines in every stage of the procedure, ranging from the filtration, filling, packaging, and storing of the final ophthalmic solution.
In conclusion, adherence to GMP guidelines is essential in the manufacturing of ear, eye, and nasal drops at CDMOs. Strict adherence to GMP guidelines ensures that the final product is of the highest quality, is consistently manufactured, and is free from contamination, which is vital to patient safety.
Akums Drugs and Pharmaceuticals Ltd.
Akums Drugs and Pharmaceuticals Ltd. is an appellation that has got recognition as a renowned contract development and manufacturing organization (CDMO) through its consistent quality and excellence. The unmatched quality states that the products manufactured by Akums bear the highest quality standards and are safe and secure to use under any circumstance. This is a result of strict adherence to GMP guidelines which authenticate it as a Who-GMP-certified pharmaceutical manufacturing firm and an efficient Contract development and manufacturing organization.
Key Takeaways
- As contract development and manufacturing organizations (CDMOs) are responsible for producing a wide variety of pharmaceutical products, it becomes paramount to adhere to Good Manufacturing Practices (GMPs) guidelines